Ethanol producer eyes 6 percent energy efficiency gain thanks to data-driven re-configuration
Small changes to ensure the beer preheater in an ethanol plant is operating within optimal performance parameters can deliver significant energy savings and increase profits. This is one focus point of Alfa Laval’s Energy Hunter programme. An ethanol manufacturer based in Northern Europe reached out to Alfa Laval when they wanted to optimize the beer preheater at their plant to increase energy savings.
DATE 2025-02-24
A detailed analysis of the existing process showed that by making simple alterations to the CIP procedure, together with adjustments to the grouping of the plate heat exchanger, the plant could increase energy efficiency by 6%.
“This is a game of big numbers,” explains Dimitrije Djordjevic, who worked with the customer to pinpoint the potential process improvements. “For customers producing between 100,000 and 500,000 litres of ethanol per day, relatively small changes can make a big impact on profits as well as carbon emissions. Saving between 500kg/h and 800kg/h of steam equates to an approximate cost saving of 400 Euros per day – so a relatively modest investment will pay back rapidly.”
Beer preheater configurations vary from plant to plant, and the suggested steps to maximize the performance of these units are customized for each production site.
“This unit has a direct impact on energy consumption, because what you don’t catch in this unit you will have to subsidize with heating energy; so indirectly, the pre-heater has an impact on the overall running costs of the plant,” says Dimitrije.
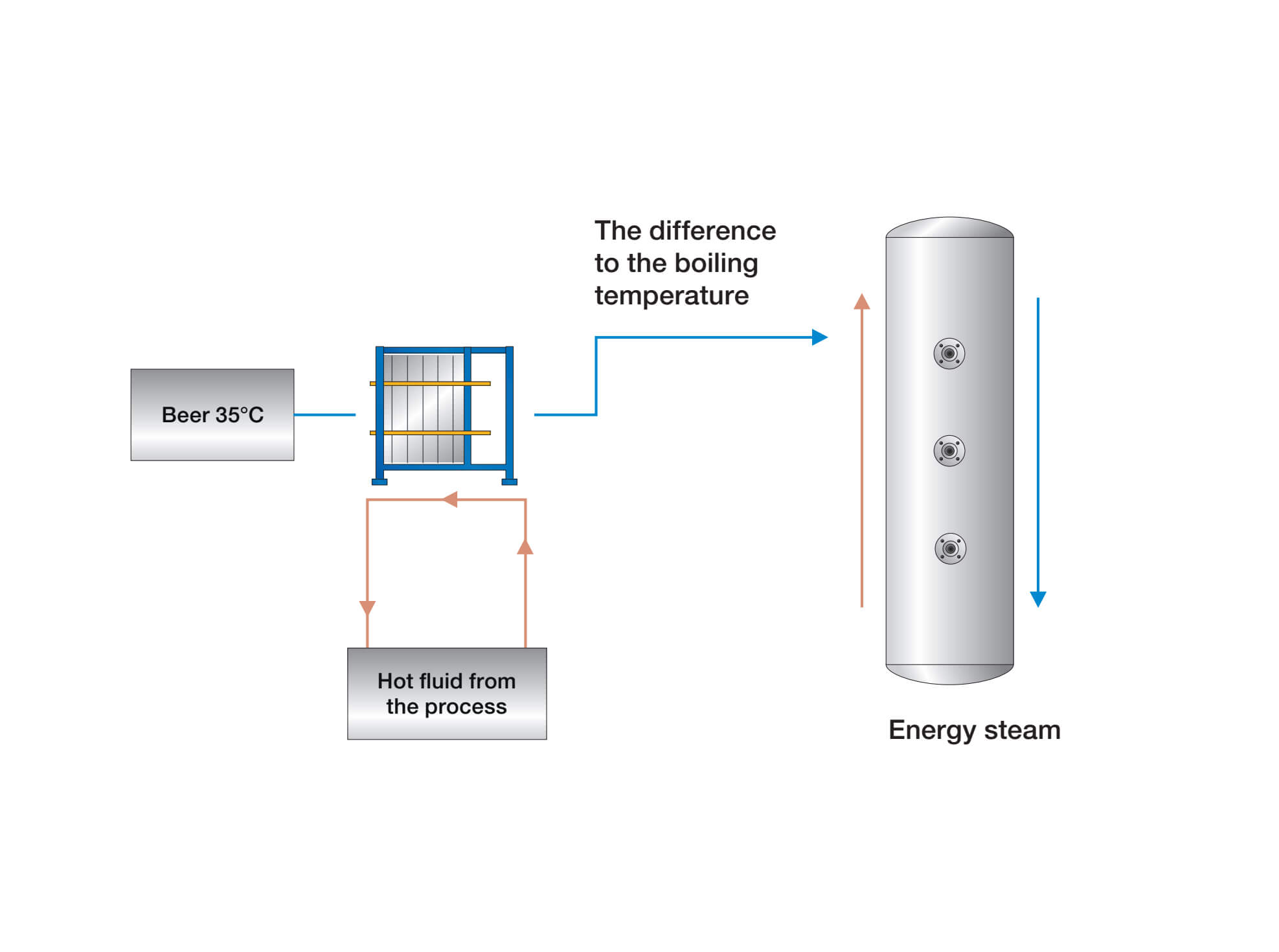
The key to success in this optimization process is a wide range of data: from plant- and process data, to data concerning PHE and CIP design, as well as numbers on energy- and material costs and CO2 emissions. The more data we gather, the more precisely we can tailor the perfect solution for our customer.
Once we have monitored the performance of the unit over time and have collected and analyzed all this information, we run it through an algorithm that generates a proposal with the optimization options available to the customer.
Dimitrije Djordjevic
Process engineer, Alfa Lava
Because each solution is tailor-made, the cost and impact of optimization will vary from case to case. Still, these are energy-hungry units, so implementing small changes with a fast payback is a win-win for customers and the planet.
And with hundreds of ethanol producers worldwide, the opportunity to positively impact energy efficiency in individual plants while also reducing global CO2 emissions is significant.
Highlighted Technologies
Energy savings
Energy saving of 6 percent
Payback time
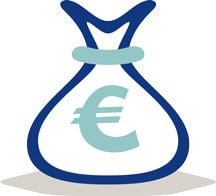
Profitability gain 400 Euros per day
CO2
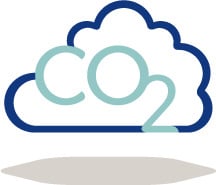
Emissions reduction