A perfect service match
A whey cheese pasteurization producer in Southern Europe, partnered with Alfa Laval to form a profitable service agreement. With a large installation of Contherm scraped surface heat exchangers and centrifuges, plate heat exchangers, pumps, and valves, a solution was established to ensure that the heat exchangers always performed at their best.
DATE 2025-03-07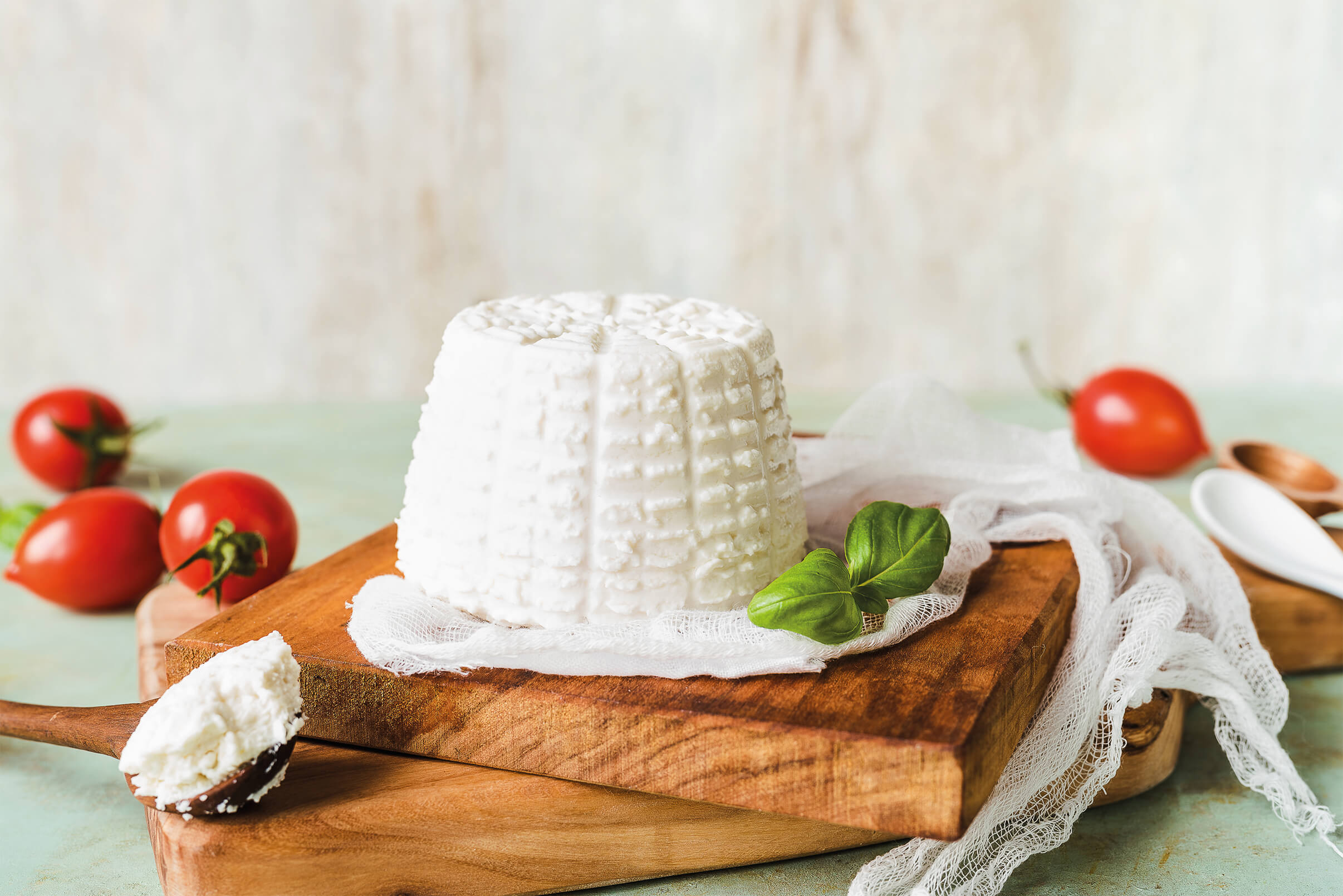
The collaboration with Alfa Laval made sure that the end user can trust extended uptime and reliable continuous production. At the same time, it eliminates uncertainty about maintenance intervals, points of inspection, necessary tools, and the fear of prolonged downtime due to equipment failure after a lack of maintenance. This is the result of a recently finalized Contherm service agreement in Europe, bringing assurance to the customer that this agreement is a perfect match.
A service agreement
To meet expectations for reliable and optimized service, Alfa Laval provided a comprehensive service agreement for the customer’s Contherm products and installation. This type of installation has the potential for severe water leakage and various process problems. Still, these can be avoided by implementing a service agreement that includes planned maintenance and risk management. Such a service agreement also offers several sustainable benefits. By preventing leakage, it is possible to conserve as much as 60 m³ of water. Additionally, efficient planning, coordination, and consolidation of maintenance activities, as well as streamlined component transportation, can lead to a noteworthy reduction in carbon footprint.
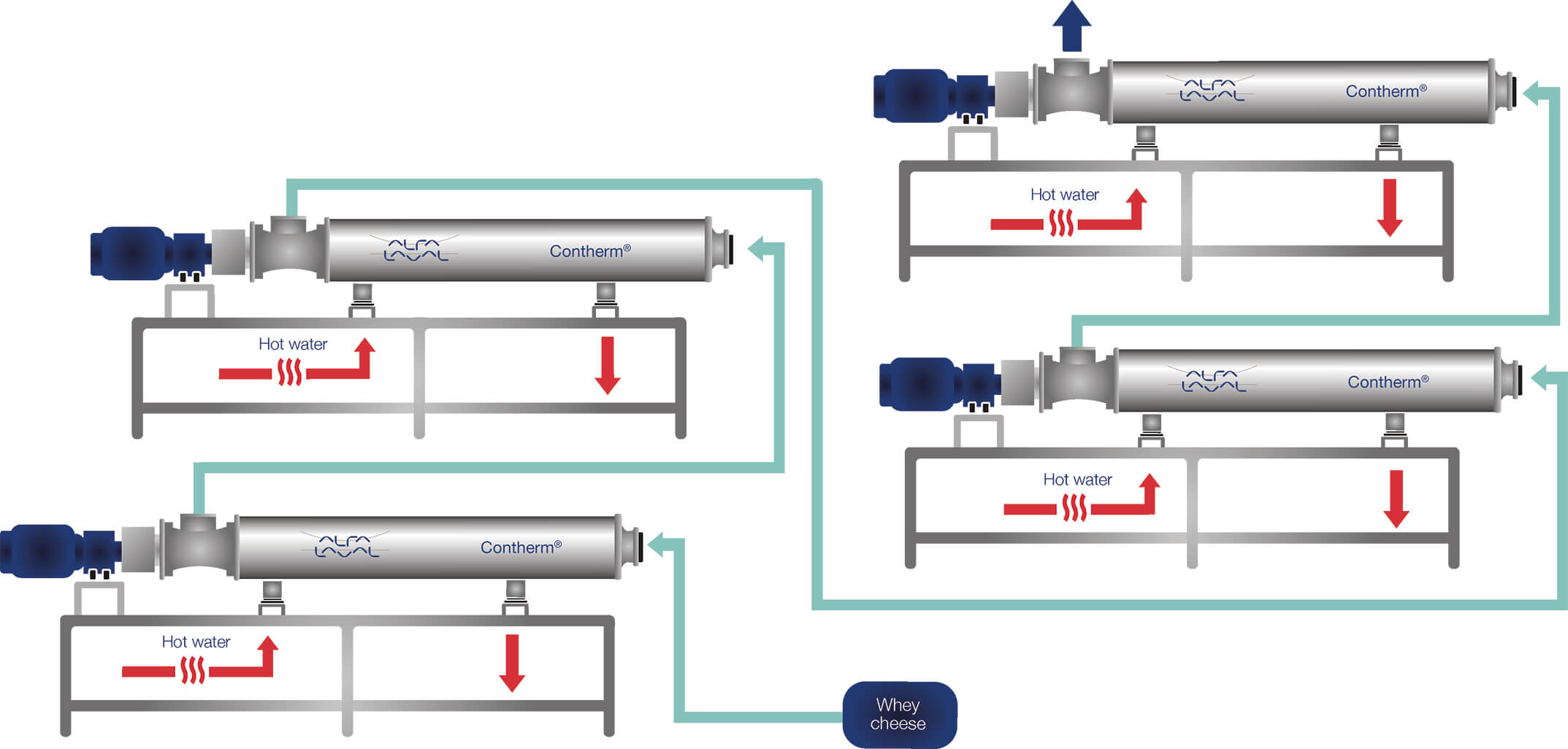
Prolonged uptime and a secure process
With the Alfa Laval service agreement, end users benefitted from the invaluable expertise of skilled personnel, ensuring optimal performance and efficiency of their equipment. A proactive maintenance approach is employed to maximize uptime and minimize unforeseen breakdowns. Collaborating with Alfa Laval to develop a customized maintenance schedule allows for a secure and optimized process while operating and maintaining the Contherm equipment.
The customer experienced significant advantages from the exceptional service, including favourable conditions, reliable parts delivery, competitive pricing, and cost-effective repairs. The ability to proactively monitor equipment conditions through condition monitoring plays a crucial role in predicting failures and extending uptime.
Giovanni Treglia, Contherm Sales Manager, Alfa Laval
CO2 savings
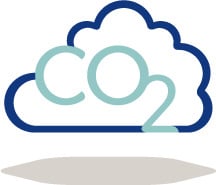
40% savings/year
Water savings
Reduced cleaning chemical consumption
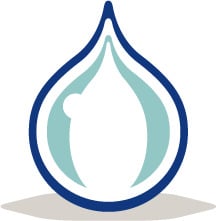
60 m3 by avoiding leakage
Uptime
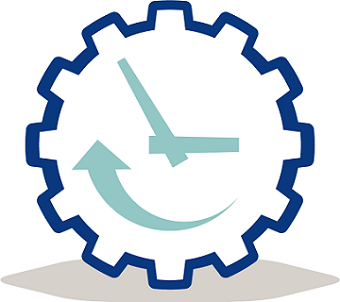
Prolong uptime by reducing risk of production stop due to unexpected failures.
Solution
- Effectively identify and address potential risks, safety concerns, and performance improvements related to the Contherm equipment.
- A comprehensive maintenance plan to ensure optimal performance, minimize unplanned downtime, and mitigate production losses, thereby reducing the total cost of ownership.
- Using Alfa Laval genuine spare parts to guarantee proper functionality, maximize uptime, and extend the lifespan of the equipment.
- Benefit from a fixed repair cost and access to stand-by items through a service tool rental and special reworking condition parts, ensuring uninterrupted production and predictable expenses.
- Enhance employee safety and minimize the risk of unplanned downtime with the Contherm Training and Remote Guidance Package. When paired with Contherm service kits, the end user can efficiently source parts and reduce maintenance time.
- Gain valuable insights into the equipment’s condition over time through the inclusion of a condition monitor in the agreement, providing a comprehensive overview for informed decision-making.