ConditionAlert™ prevents critical failure in a bioethanol plant
A bioethanol plant in the US faced a recurring challenge with frequent bearing failures, leading to significant disruptions in their operations. Recognizing the critical importance of uptime, the customer made the strategic decision to create a dedicated department focused on ensuring equipment uptime and preventing future failures – and reducing their carbon footprint in the process.
DATE 2025-02-24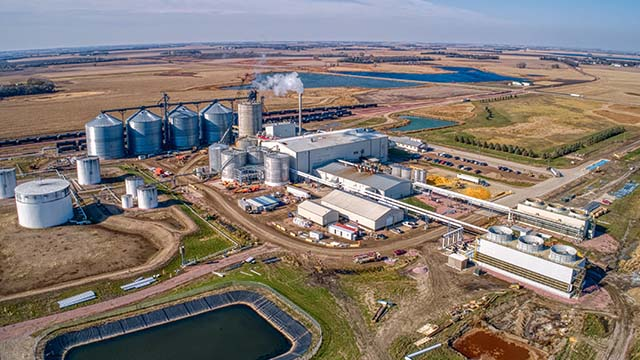
To tackle the bearing failure issue, the customer implemented ConditionAlert™, from Alfa Laval's Connected Services, a comprehensive condition monitoring system, on three key machines in August 2020. ConditionAlert™ continuously monitored specific decanter components, utilizing four different vibration levels as indicators.
From the time of installation, ConditionAlert™ diligently monitored the machines around the clock, with no specific findings until April 2021. At this point, ConditionAlert™ detected an increase in vibration levels in the decanter bearing, prompting multiple reports to be sent to the customer. These reports provided a clear diagnosis and actionable recommendations to sustain proper operations until May 2021. The recommendations highlighted the need for immediate machine stoppage and bearing replacement to prevent an impending critical failure.
The implementation of ConditionAlert™ yielded substantial benefits for the customer:
- Cost Savings: The prevention of bearing failure and potential crash resulted in cost savings of more than 25,000 EUR. This includes savings from avoiding the repair costs associated with the decanter and any consequential damages caused by a failure event.
- Reduced Downtime: Instead of facing several days or weeks of downtime for repairing the decanter after a crash, the customer experienced only one day of downtime to replace the damaged bearing onsite. This significant reduction in downtime minimized the impact on the plant's overall operations and productivity, and so offered a sustainability boost through more efficient operations, CO2 savings and less travel time required by resolving the issues before they became more serious.
- Improved Maintenance Planning: Leveraging the diagnostics and recommendations provided by ConditionAlert™, the customer was able to proactively plan service activities and together with Alfa Laval secured the availability of required parts well in advance. This proactive approach enhanced maintenance efficiency, minimized disruptions, and ensured smoother operations.
Through the implementation of Alfa Laval's Connected Services and the adoption of ConditionAlert™, the bioethanol plant successfully addressed their recurring bearing failure challenge. The continuous monitoring and timely diagnosis offered by ConditionAlert™ played a crucial role in averting a critical failure, resulting in considerable cost savings, reduced downtime, and enhanced maintenance planning for the customer. This case study exemplifies the tangible value delivered by Connected Services, showcasing its efficacy in ensuring equipment uptime and optimizing operations for industrial plants facing similar challenges.
Highlighted technologies
Decanter connected services
Corn ethanol’s carbon footprint is currently a third less than gasoline and continues to decrease with increased carbon-conscious efforts from corn growers and ethanol plants. As part of the efforts to achieve sustainability and mitigate climate change, the industry aims to minimize the environmental impact of corn ethanol production. This includes implementing practices and technologies that result in lower greenhouse gas emissions throughout the entire lifecycle of corn ethanol. One approach that some corn ethanol plants are turning to is connectivity, leveraging digital technologies to optimize operations and minimize their carbon footprint.
Cost savings
The plant saved over 25,000 EUR
Reduced Downtime
Several days saved of unplanned downtime