Alfa Laval turns up the heat to brew a sustainability boost
Recovering additional heat in the brewing process has generated significant efficiency improvements at a brewery in China, resulting in substantial energy and cost savings in their operations.
DATE 2025-04-23
In fact, the Carlsberg facility in Xichang is enjoying a number of benefits now that they are operating with Alfa Laval’s T25 gasketed plate heat exchanger (GPHE) as a vapour condenser, recycling hot water produced from wort vapour and using it to pre-heat the next wort batch. Total steam consumption of wort pre-heating and boiling has dropped by around 10% as a result.
On this project, Alfa Laval worked with the integrator Zhejiang Chengxin Mechanical Technology Co Ltd. The system builder has enjoyed a long-term cooperation with the end user, so when Carlsberg indicated the high importance of sustainability gains as a project driver, they came to Alfa Laval.
Positive impact on the operation
The replacement of the old shell and tube (S&T) vapour condenser with Alfa Laval’s GPHE technology has had a significant positive impact on the operation, principally through increasing the temperature of the heating water at this key point in the process by around 4°C.
It means less steam is required to get the wort to boiling point at the next stage in the process and means the brewery moves forward with a sustainable solution. In the first five months of operation Carlsberg reduced steam consumption by 314 kg per batch, so with eight batches a day over 300 days annual operation, this adds up to a saving of 750 tonnes of steam or 727 MWh per year, and reduces annual CO2 emissions by nine tonnes.
Simon Ning, Alfa Laval China Sales Manager, explains: “The customer is very satisfied with the performance and the heat recovery. With the old shell and tube, the water could only be heated to 95 degrees but with the new unit the customer can heat the water to around 98-99 degrees, so the performance is very good.”

Tom Zhao, General Manager of Carlsberg Xichang, said they were surprised and delighted with the impact of their new equipment. He says: “Initially we thought the main benefit of the heat exchanger would be the compactness of it, and the space we would be saving as a result. However, once we discussed the potential of the technology with the Alfa Laval team, we understood that this was bringing so much more to the process in terms of saving energy and costs.
Fast delivery and space saving
From those initial discussions to the delivery of the solution took only four to five months and as well as delivering energy savings through a more efficient process, the unit has also delivered on space-saving expectations by being more compact, as a new S&T solution would have taken up much more factory space. The installation is also set to have a significant impact on main[1]tenance – so saving yet more time, resource, and cost.
“Another pain point with shell and tube is the cleaning,” explains Simon’s colleague Nancy He, Technical Support Alfa Laval China. “S&T heat exchangers are very difficult to clean and with our GPHEs, for this customer, they have already done cleaning in place (CIP), which they didn’t do previously. This means they can clean the system without lengthy delays which saves on time, and the thermal performance of the unit is maintained at a very high level. Control feedback from this unit is also faster than S&T.”
Such has been the success that more opportunities are set to follow, as Simon explains: “This case has been so successful that the integrator wants to promote this solution to other cus[1]tomers; replacing older S&T units for our GPHE technology, and we are already moving forward with the integrator on another two projects.”
Highlighted technologies
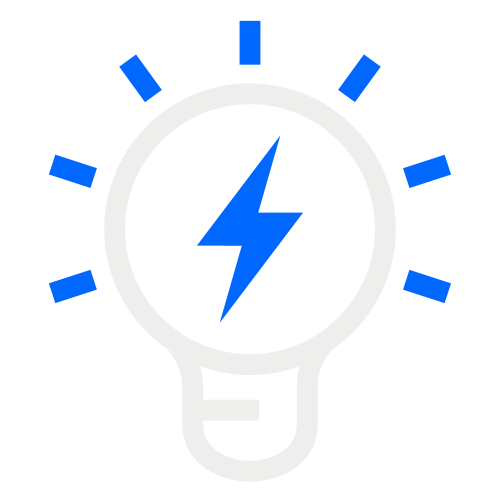
Energy savings
727 MWh/year

CO2e savings
9000 kg/year