De-alc de-alcoholization module
Remove the alcohol—keep the experience. Alfa Laval De-alc de-alcoholization module delivers less than 0.05% ABV while preserving the full flavour and aroma of any beer, wine, or beverage. This compact, energy-efficient module simplifies production, boosts yield, and creates new revenue opportunities. A smart, sustainable way to meet rising demand for no- and low-alcohol beverages.
100% flavour, zero compromises
- Diversify your production with a single system
- Zero product loss
- Better for the planet and your bottom line
- Stay safe and compliant without the complexity of explosion-proof zones
Meet rising demand for alcohol-free beverages without compromising taste or quality. Alfa Laval De-alc gently removes alcohol while preserving the full sensory experience of your product.
Easily expand your product range with new recipes and styles. Unlike traditional distillation, which exposes the product to high temperature for several minutes De-alc removes the alcohol in under a minute. Its plug-and-play design enables quick installation, low maintenance, and high uptime.
Reduced water use, optional aroma recovery, and alcohol reuse add value. With seamless CIP integration and no need for explosion-proof zones, cleaning and compliance are safe, easy and cost-effective. The De-alc is backed by Alfa Laval’s global service network.
Integrating the De-alc module into our production lines not only helps Asahi meet its sustainability objectives but also strengthens our competitive edge,
– Mr. Jun Kubota, Global Chief Brewer at Asahi Group Holdings
How the De-alc de-alcoholization module works
The Alfa Laval De-alc module uses a compact, fully automated process to gently remove alcohol from beer at low temperature and pressure—preserving quality, flavour and aroma. The system integrates all key process steps, from degassing and aroma recovery to stripping, condensation, and final chilling.
Degassing and aroma recovery
The process begins with degassing the feed beer in a low-pressure chamber. This reduces carbonation and prevents foaming in the stripping column. Volatile aroma compounds released during this step are captured in a chilled separator and returned to the beer or beverage stream, preserving its full sensory character.
Alcohol stripping in vertical column
Next, the product enters a vertical stripping column packed with proprietary Alfa Laval material. It flows downward while culinary steam rises from the base, creating a counter-current flow under near-vacuum conditions. This setup ensures efficient alcohol removal by maximizing contact between steam and product — achieving high desorption at low temperature and pressure. Regulating flow through automated control ensures uniform distribution via a liquid distributor at the column’s top.
Vapour condensation and recovery
Alcohol-rich vapour exits the column and passes through a plate heat exchanger, where it condenses into a liquid stream. Removal of any remaining non-condensable gases takes place in a vacuum phase. A glycol-side recirculation pump ensures reliable operation by preventing freezing in the condensation stage.
Gentle heating with energy recovery
A plate heat exchanger with recirculated hot water heats the product to the required stripping temperature. To reduce thermal input and operating while protecting product quality, the outgoing de-alcoholized beer preheats the incoming feed beer, efficiently recovering energy.
Optional recirculation for additional stripping
While the system typically achieves the target ABV in a single pass, a integrated recirculation loop allows for additional stripping if needed. Stripping performance can be further optimized by adjusting beer temperature or stripping column pressure.
Culinary steam generation
An integrated steam generator produces culinary-grade steam by heating soft water in a shell-and-tube or plate heat exchanger. This steam, injected at the base of the column, acts as the stripping gas.
Final cooling
The final step cools the de-alcoholized product to the required outlet temperature using the glycol-fed section of the module’s heat exchanger. The design prevents freezing and ensures stable, energy-efficient cooling.
Latest customer success stories
You might also be interested in...
Service
Food system services
Alfa Laval Food system services help extend the performance of your food systems by maximizing the performance of your processes. This enables you to:
- Continually improve your operations to maintain competitive advantage
- Focus on uptime, optimization and availability
- Maximize return on investment throughout the life cycle of your food systems
Be inspired
There is a steady, substantial and global move towards beers featuring less alcohol. Some brewery experts reckon that by 2020 as much as 20% of all the beer sold will fall into the so-called “healthy” category. For “healthy”, read “with alcohol content removed”. But how can one use the removed alcohol?
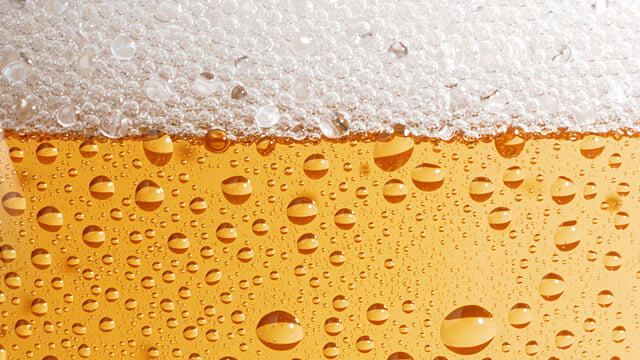