Troubleshooting for plate heat exchangers
Are you experiencing issues with your gasketed plate heat exchanger? Is there leakage outside the unit, leaking within the unit or unexpected pressure drops? Identify possible causes with our online troubleshooter!
If you need further support our experienced and skilled troubleshooters are at your service and provide immediate on- and offsite support, to solve any issue related to your equipment. We find the cause of unplanned shutdowns and make sure equipment performs as well as possible. We also identify and prevent hazardous situations, to improve working conditions for your staff.
Leakage issues
You may experience various leakage issues with your heat exchanger units. With the simple troubleshooter, we hope we are able to help you identify the causes of your issues and can solve some of those problems with our guided steps. Alfa Laval can help you with:
- Material selection and test
- Parts replacement
- Reconditioning
- Visual conditioning
- Assessment
- Condition audit
What leakage issues are you experiencing with your gasketed plate heat exchanger?
Gasket leaking due to aging Media leaking externally, while gaskets are visible partially on the side of the plate pack Swelling or dissolving of gasket
Media leaking externally, gaskets are cracked and pushed out from the side External leaking and gaskets hang loosely while open
I can see that the leakage may be caused by aged gaskets. The gaskets are hardened, there are cracks on them, and cold leakage indicates problems.
Possible causes:
- Material failure due to age or high temperature
- Oxidant present in the process stream
- Unsuitable or over-concentrated cleaning liquid
- NBR density to Ozone
Proposed solution:
- Replace gaskets if age is the cause. Check gasket compatibility with the media and upgrade the material if necessary. You can also perform a full reconditioning at your nearest Alfa Laval service centre.
- If the CIP (Cleaning-in-Place) is the root cause then review method and cleaning liquid.
For future prevention:
- Replacing gaskets at recommended intervals will prevent failures due to age.
- In other circumstances, consider changing to a different elastomer to ensure media compatibility or a change in plate alloy to prevent corrosion.
Did these suggestions help? If not, contact us by phone or mail.
My unit's media is leaking externally. the gaskets are partially visible on the side of the plate pack.
Possible Causes:
- Hydraulic hammering, gasket swelling due to incompatibility with the media, or deformed gasket grooves.
- Un-tightened plate pack.
- Clogging in combination with high pressure.
- Broken glue bond in combination with high pressure.
Proposed solution:
- Perform re-gasketing or upgrade to an epoxy fastening system.
- Ensure gaskets are compatible with process and confirm that no deformations exist in the gasket groove.
- Check start-up procedures, process, pumps and valves.
For future prevention:
- Follow Instruction-Operating Manual for proper start-up and shutdown procedures.
- When opening valves, open the outlet first and then slowly open the inlet. Be careful not to overtighten the heat exchanger and make sure that the unit is tightened according to the recommended A-dimension to ensure metal-to-metal contact.
Did these suggestions help? If not, contact us by phone or mail.
There is swelling or dissolving of gasket in my unit. It is difficult to seal a unit after opening.
Possible causes:
- Absorption of process media or cleaning liquid.
- The gasket is not compatible with media.
Proposed solution:
- Change to different elastomer material that is suited to the media.
- Review selection of cleaning media.
For future prevention:
- Provide media and water quality report, prior to purchase for the best “recommended” gasket material.
Did these suggestions help? If not, contact us by phone or mail.
My unit's media is leaking externally. The gaskets are cracked and pushed out from the side. Pieces of rubber are missing.
Possible causes:
- A crack is initiated and propagates through the rubber material.
- The gasket not placed in the centre of the gasket groove but on the edge.
- Aggressive media "eating" away of the material.
- Volume increases due to high temperature.
Proposed solution:
- Change the gaskets and consider upgrading to a different material.
- Follow instructions for gasket change and closing of unit.
- Ramp up temperature above 100C if possible
For future prevention:
- Follow Instruction-Operating Manual for proper start-up and shutdown procedures.
- Provide proper training to operators.
Did these suggestions help? If not, contact us by phone or mail.
My unit has external leakage and/or gaskets hang loosely when opening the plate pack.
Possible causes:
- For glued units
- Glue bond failure
- Plate gasket groove dirty
- Gasket dirty
- Unsatisfactory curing of the glue
- Unsuitable glue for the process
- For glue-free units
- Dislocation
- Wrong assembly
Proposed solution:
- On minor parts use repair glue and if major consider performing full reconditioning of the plate pack with correct glue and procedure.
- Place the glue-free gasket correctly in the groove, you may have to use tape to fix and carefully close it.
For future prevention:
- Make sure to clean the gasket, clean the gasket groove, follow curing instructions and check the gasket is sitting fixed in the right spot.
- Review glue type.
- Check that the gasket is in the groove and carefully close it.
- Provide proper training to operators.
Did these suggestions help? If not, contact us by phone or mail.
Performance issues
You may experience performance issues such as cyclic performance deviating, gradual performance deviating as well as immediate performance deviating. Alfa Laval can help you with:
- Redesign and optimization
- Visual condition assessment
- Performance audit
- Cleaning in Place
- Parts replacement
- Condition audit
- Reconditioning
- Inspection
- Training
- New unit
What performance issues are you experiencing with your gasketed plate heat exchanger?
High pressure drop or reduced thermal performance - cyclic performance deviating
Pressure drop or reduced thermal performance - gradual performance deviating Process media leaks into the utility media or vice versa
Pressure drop or reduced thermal performance - immediate performance deviating Uneven temperature distribution
Pressure drop or reduced thermal performance - possibly media leaking
I experience high pressure drop or reduced thermal performance that impacts the system efficiency. It is cyclic performance deviating.
Possible causes:
- Seasons variations in temperature or unstable process.
Proposed solution:
- Confirm the actual parameters versus the parameters with the original the heat exchanger’s design.
- If considering re-design or optimization, review channel plate wall sheer stress or alternate plate pressing options.
For future prevention:
- Careful evaluation during design stage considering best possible solution taking into account temperature variations during the year.
Did these suggestions help? If not, contact us by phone or mail.
I experience high pressure drop or reduced thermal performance that impacts the system efficiency and/or uptime. It is gradual performance deviating.
Possible Causes:
- Accumulation of undesired substances on a surface.
- Low sheer stress on plate channel walls.
- Operating conditions differ from design parameters. Chemical reactions, precipitation etc. Possible mal-distribution when PHEs are in parallel.
Proposed solution:
- Perform chemical or mechanical cleaning.
- Confirm the actual flow rate is consistent with the intended flow rate of the heat exchanger’s design.
- Consider re-design or removing plates, review channel plate wall sheer stress or alternate plate pressing options.
- Consider installing inline filters.
For future prevention:
- Optimized cleaning-in-place (CIP) procedures carried out according to instructions is the smartest way to address fouling.
- You can also remove plates to increase sheer stress, enhance the heat transfer surface area, or consider different pressing depths for the plates.
Did these suggestions help? If not, contact us by phone or mail.
My unit's process media leaks into the utility media or vice versa. This has caused minor change in thermal conductivity. It is gradual performance deviating.
Possible causes:
- Either corrosion or fatigue cracking has resulted in a hole on the plates of the heat exchanger.
Proposed solution:
- Perform a hydro test with plates installed in unit. Open the opposing port hole to check for bubbling water, which will tell you the location of the leak.
- Consider upgrading the plate material with alternate alloys. If the issue is fatigue-related, check for operational pressure spikes or surges.
For future prevention:
- Avoid pressure spikes or surges, and make sure you select correct alloy during the initial design phase.
Did these suggestions help? If not, contact us by phone or mail.
I experience high pressure drop or reduced thermal performance that impacts the system efficiency and/or uptime. It is immediate performance deviating.
Possible causes:
- The size of particulates in the media exceeds the pressing depth of the channel plates.
- Foreign debris is present in the stream.
Proposed solution:
- Identify the largest particulate size and quantity in the media.
- Backflush the filter, install inline filters or consider alternate plate pressing depth.
For future prevention:
- Install port filters or strainers if debris is larger then 50% of the free channel. Another option would involve an upgrade to plates with a larger free channel (e.g. wide gap plates).
- Before starting up the process (first time or after system service stops) flush pipes to ensure any foreign debris does not enter the PHE.
Did these suggestions help? If not, contact us by phone or mail.
There has been uneven temperature distribution over the unit starting as soon as the flow rates create conditions for maldistribution. Outlet temperature differ between parallel units. It is immediate performance deviating.
Possible causes:
- Un-even flow distribution caused by operating conditions differing from design parameters.
- Wrong design.
Proposed solution:
- Re-design to achieve a more even flow distribution over the parallel units (or take out one unit).
- If it is in one unit consider replacing with a larger port size or add a unit in parallel.
For future prevention:
- Always check actual conditions versus design parameters carefully.
Did these suggestions help? If not, contact us by phone or mail.
I experience high pressure drop or reduced thermal performance that impacts the system efficiency and/or uptime. I can observe media leaking in my unit. It is immediate performance deviating.
Possible causes:
- This may be due to wrong assembly of plates. The plates may have been assembled wrongly or in wrong order after a service stop.
- It could be due to incorrect assembly or using wrong parts during manufacturing.
Proposed solution:
- Check the honey comb pattern on the side of the GPHE to ensure it is uniform.
- Check and verify the heat exchanger specification versus documentation delivered with the heat exchanger.
- Open the heat exchanger and confirm the plates hand in the same order as per the plate hanging list.
For future prevention:
- When doing a service mark the side of the plate pack with a diagonal line and/or number each plate in the correct order they hang in the heat exchanger.
- Always follow the instruction manual and the plate hanging list.
Did these suggestions help? If not, contact us by phone or mail.
Damaged parts
Your heat exchanger units may get damages. With the simple troubleshooter, we hope we are able to help you examine your unit if it is damaged with a few symptoms. Alfa Laval can help you with:
- Assessment
- Parts replacement
- Training
What type of damage are you experiencing with your gasketed plate heat exchanger?
Damages on plate/ plate pack Damages on frame/ frame parts Damages on gaskets
I can spot damages such as deformations, marks, scratches, rust, snaking, etc. on plates and plate packs.
Possible causes:
- It may have been dropped or hit by truck/tool during transport or during handling at site.
- Rust can be normal wear and tear depending on environment and age. The damage may not have caused the unit to leak (yet) and some damages will not actually harm the performance.
Proposed solution:
- Record the damages, check the instruction manual for guidelines.
- Make a risk assessment and if deemed safe you may consider doing a leak test to the operating temperatures.
- If necessary plan service at next service interval.
For future prevention:
- Handle your heat exchanger unit with care.
- Use the correct tools and always follow the guidelines in the instruction manual.
Did these suggestions help? If not, contact us by phone or mail.
I can spot damages such as deformations, marks, scratches, rust, snaking, etc. on frames/ frame packs.
Possible Causes:
- It may have been dropped or hit by truck/tool during transport or during handling at site.
- Rust can be normal wear and tear depending on environment and age. The damage may not have caused the unit to leak (yet) and some damages will not actually harm the performance.
Proposed solution:
- Record the damages, check the instruction manual for guidelines.
- Make a risk assessment and if deemed safe you may consider doing a leak test to the operating temperatures.
- If necessary plan service at next service interval.
For future prevention:
- Handle your heat exchanger unit with care.
- Use the correct tools and always follow the guidelines in the instruction manual.
Did these suggestions help? If not, contact us by phone or mail.
I can spot damages such as deformations, marks, scratches, rust, snaking, etc. on gaskets.
Possible causes:
- It may have been scratched during handling at site.
- Cracks or hardening can be normal wear and tear depending on environment and age (ozone cracks). The damage may not have caused the unit to leak (yet) and some damages will not actually harm the performance much (shorter life).
Proposed solution:
- Record the damages, check the instruction manual for guidelines.
- Make a risk assessment and if deemed safe you may consider doing a leak test to the operating temperatures.
- If necessary plan service at next service interval.
For future prevention:
- Handle your heat exchanger unit with care.
- Use the correct tools and always follow the guidelines in the instruction manual.
Did these suggestions help? If not, contact us by phone or mail.
Making efficiency last for decades
A poorly functioning heat exchanger may affect safety, product quality and energy costs. Failure may lead to costly downtime and major losses in production. By regular and proactive maintenance of your gasketed plate heat exchanger performance is preserved and operations kept trouble-free and predictable.
We have the expertise to help you whether you experience a problem today, wish to prevent future issues or want to solve the problem yourself with our online troubleshooter.
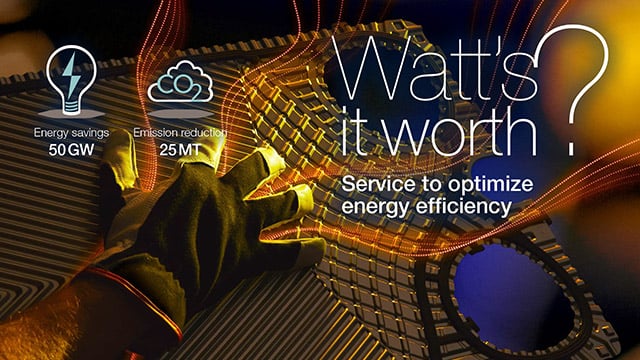
Service to optimize energy efficiency
Every year, the number of heat exchangers we service to optimize energy efficiency reduces our customers’ capacity needs by 50 GW. That is the amount of energy that can be generated by 10,000 wind turbines in the same timeframe.
In carbon emissions, 50 GW translates to a 25 million tonne reduction to our global footprint, or the carbon emitted by the city of London every year.
Imagine what we could achieve if the world’s industries regularly serviced their plate heat exchangers to optimize heat transfer efficiency.